Sand Casting Services in Rajkot – We Cater to Your Versatile Requirements.
We at Noble Engineers bring a specialized solution for Sand casting. It is a process based on the industrial techniques ofresin Sand Casting.
Our offerings are not limited to Rajkot. We offer a comprehensive service solution and customized casting techniques for industries across India.
Precise size and design with Resin Sand Investment Casting is our specialization! With us, you can find industry-specific casting solutions for Automotives, Marine and lpg burner industries, machine and equipment manufacturers, etc.
Our team of proficient members has years of experience and expertise in investment casting Rajkot. With us, find casted products of the following types and more – Resin Sand Castings with an overall weight of up to 100 Kg/Pcs capacity and size of up to 1200 x 1200 x 500 mm. -We employ the Roll-over technology for our manufactured products with a maximum casting weight of 100Kg. – wehave capacity of 1500-2000 tones per annum.
One - Stop Solution for Sand Casting In India
Over years, we have emerged as a trusted partner for Resin Sand Casting requirements. We are the leading sand casting suppliers cum manufacturers in Rajkot, delivering appropriate and accurate accessories for diverse industrial needs.
We export – Find tailor-made solutions for resin sand casting in different parts of India. We have an extensive network and have emerged as the most-trusted sand casting Exporters in the industry.
We manufacture – Our team uses roll-over technology to deliver accurate dimensions and utility of the products. Rely on our specialized techniques to fetch the services of the top-class sand casting manufacturers in India.
We supply – We let our clients express their requirements and prioritize their demands. Thus, we have emerged as the supreme choice for sand casting suppliers across all heavy-duty industries.
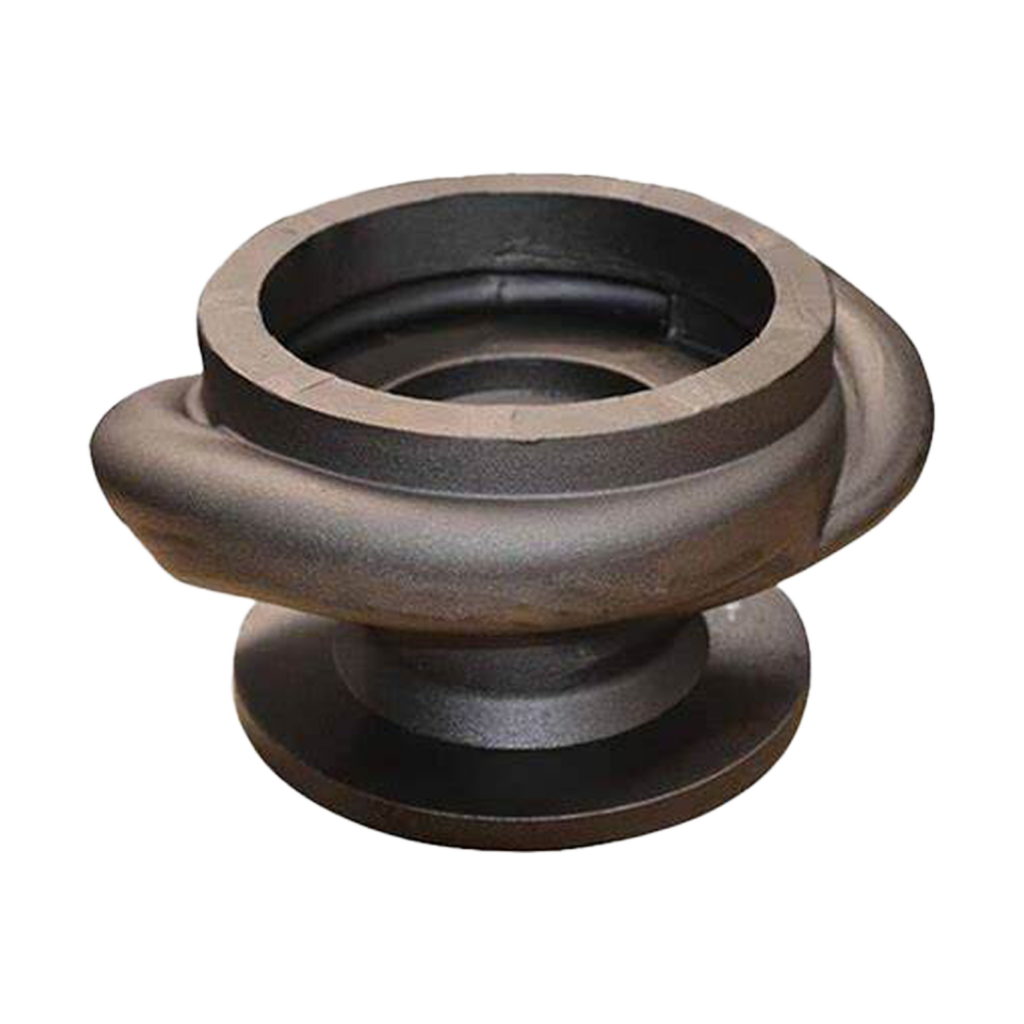
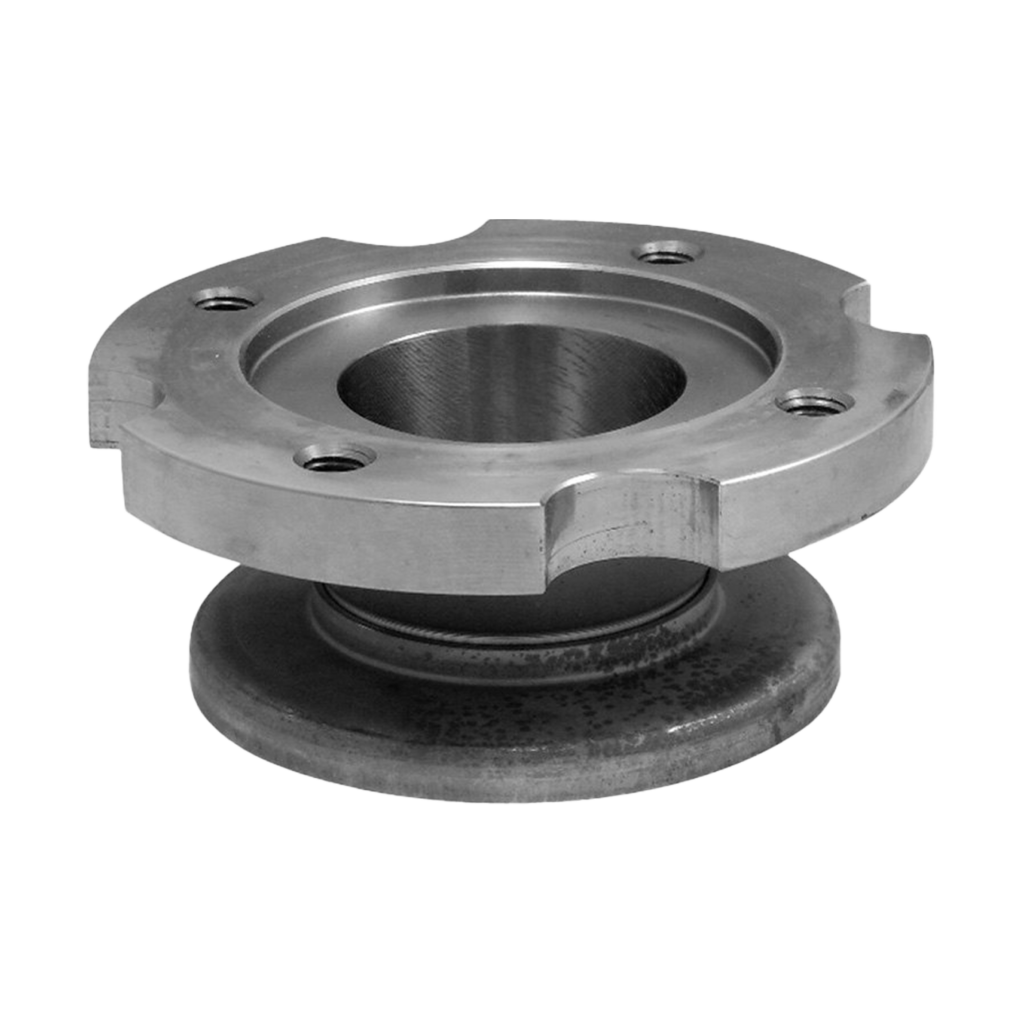
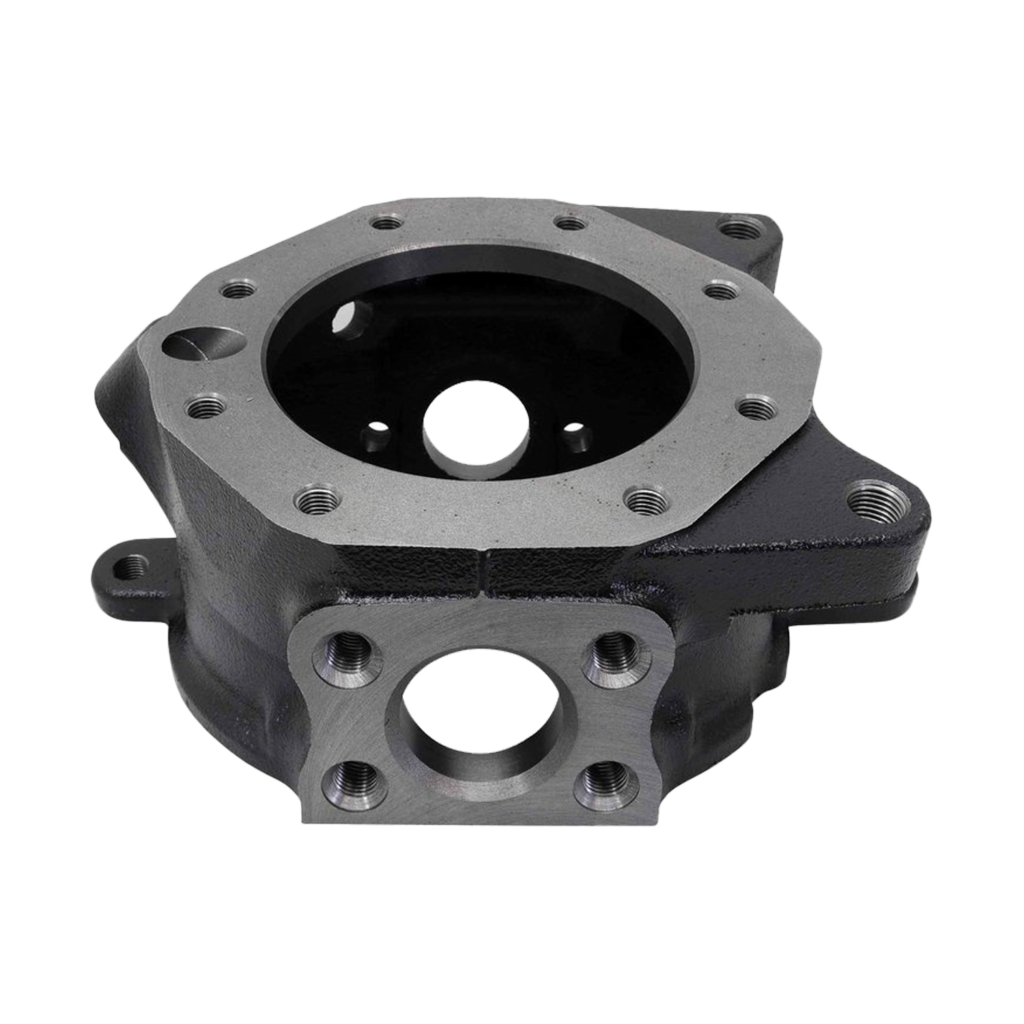
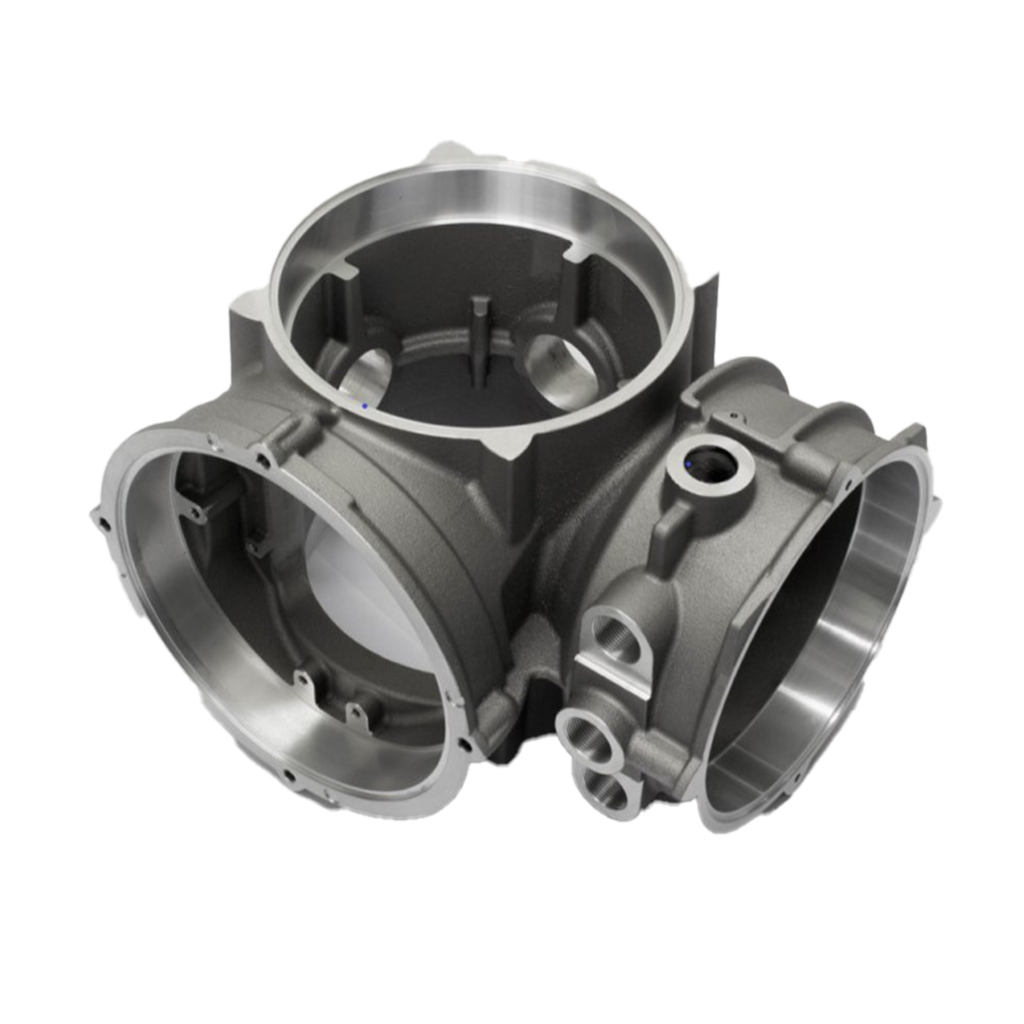
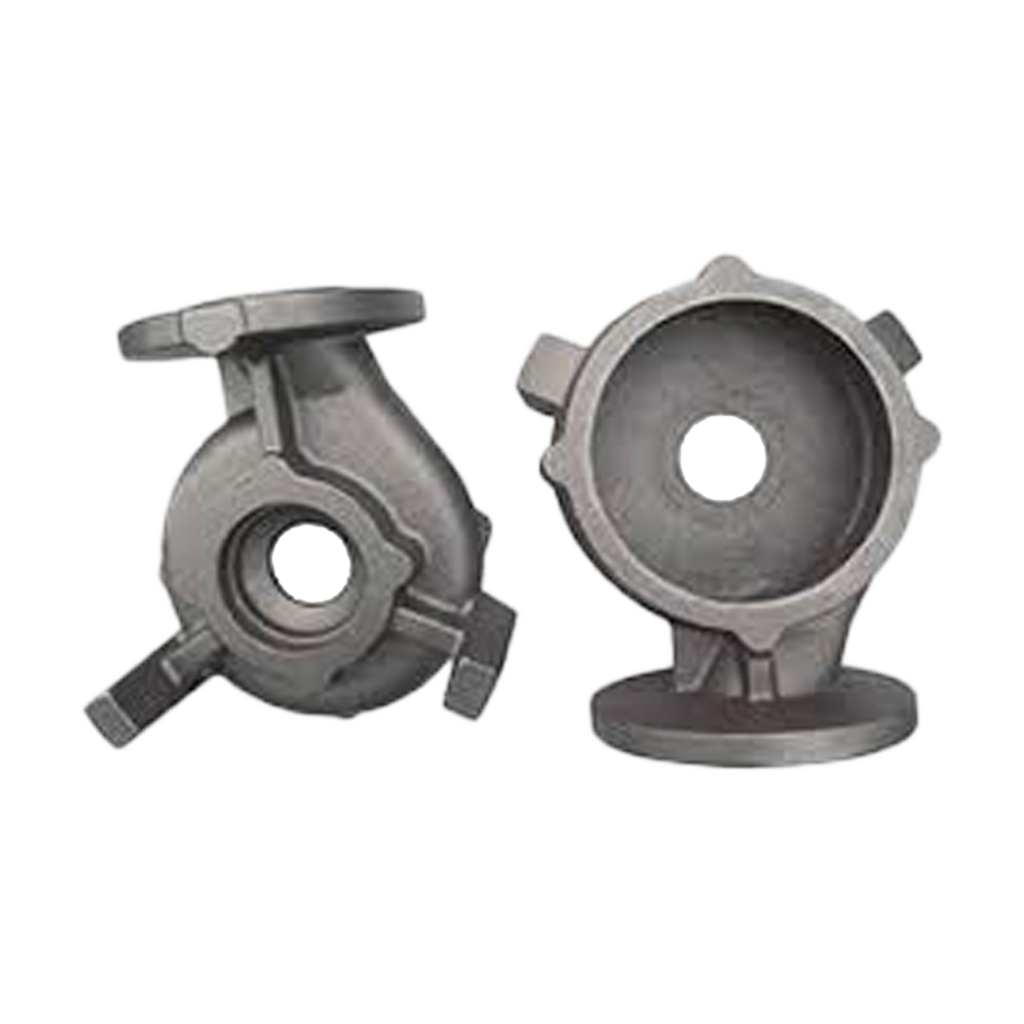
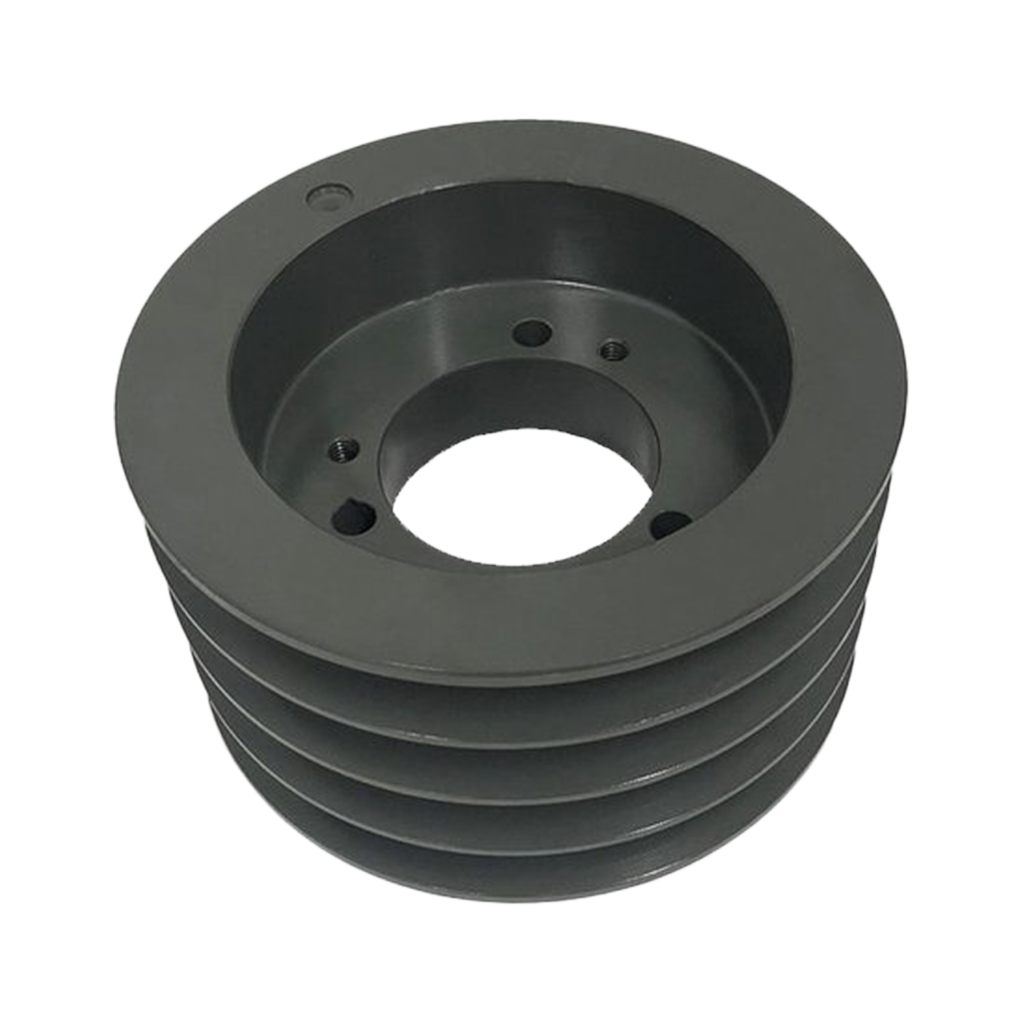
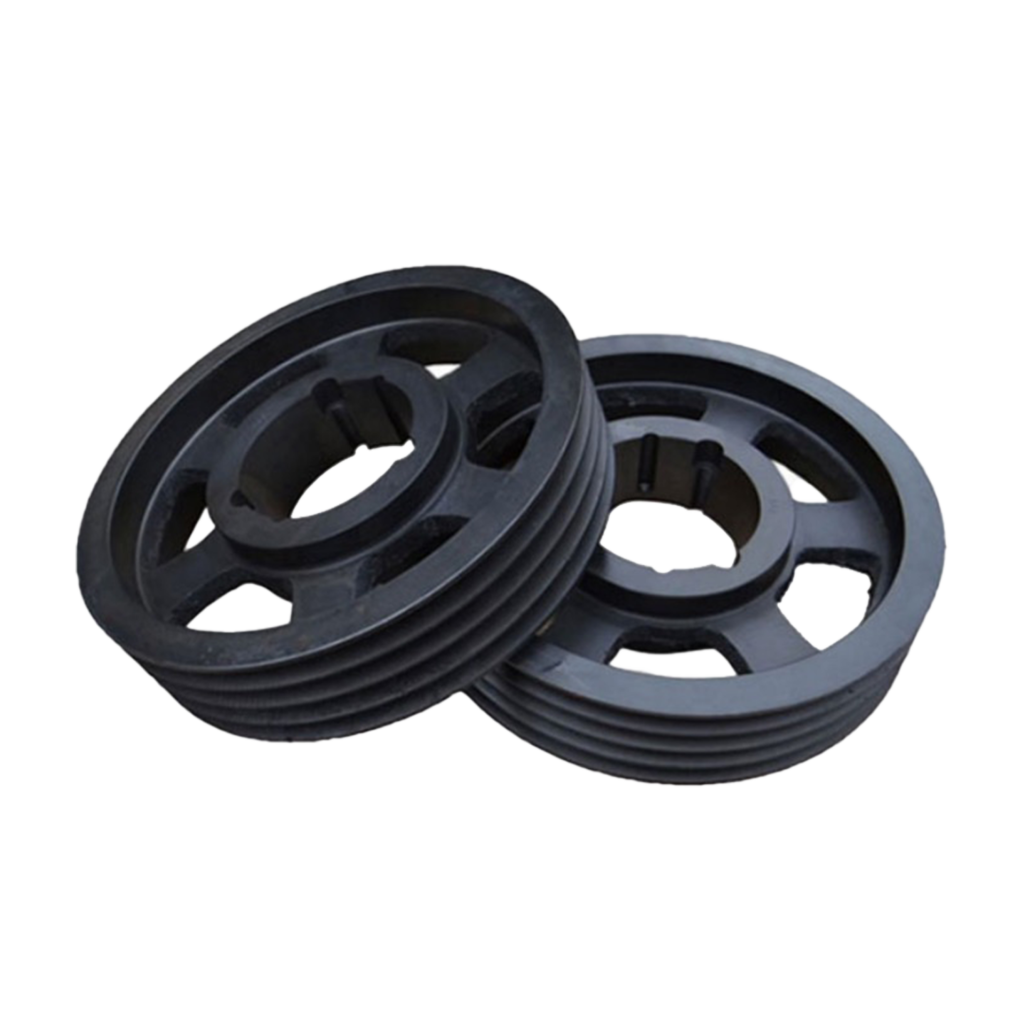
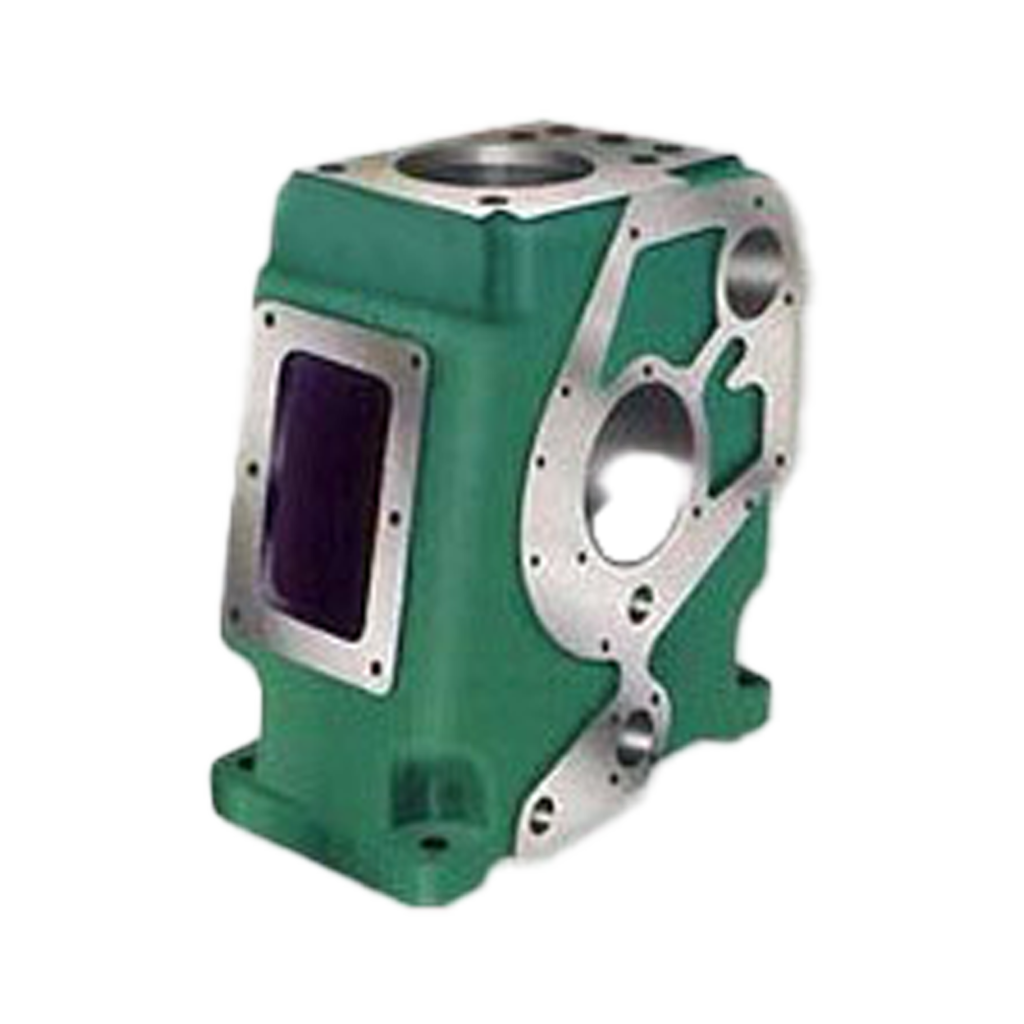
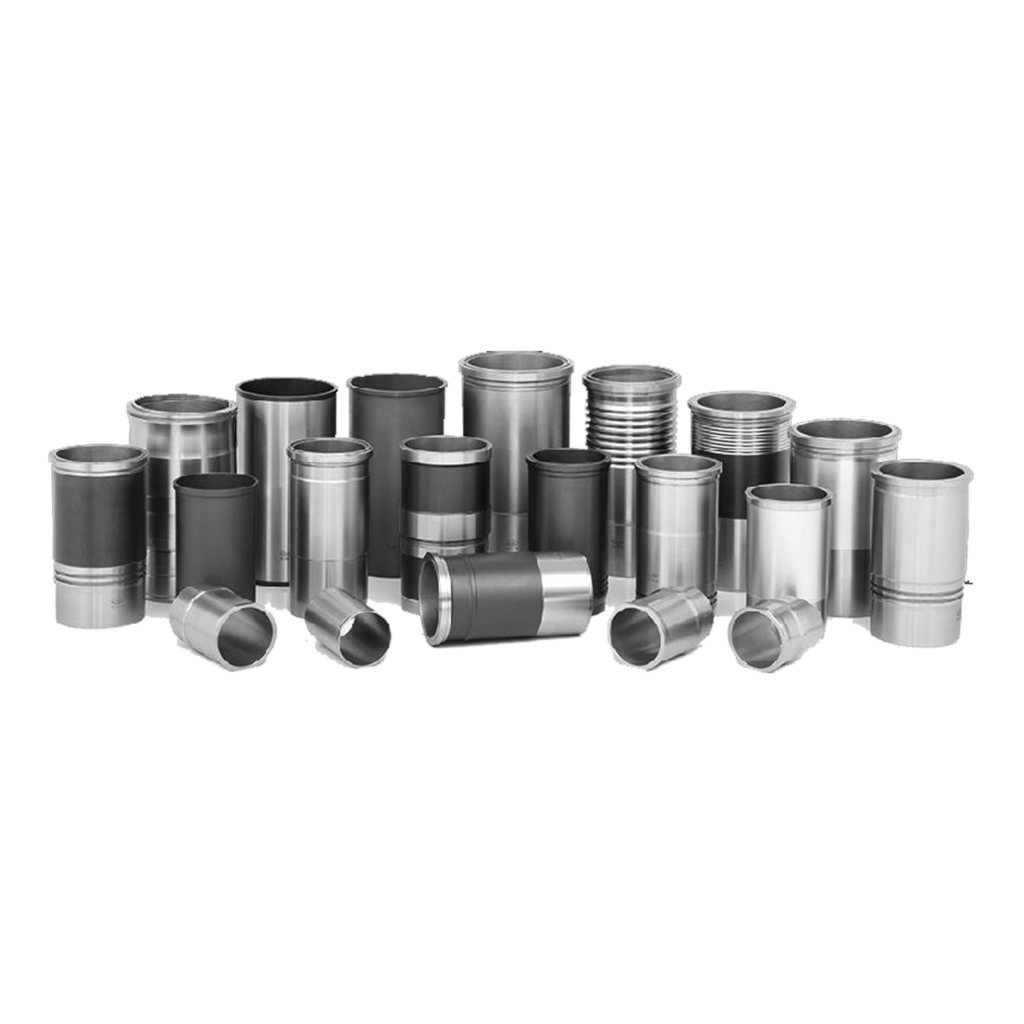
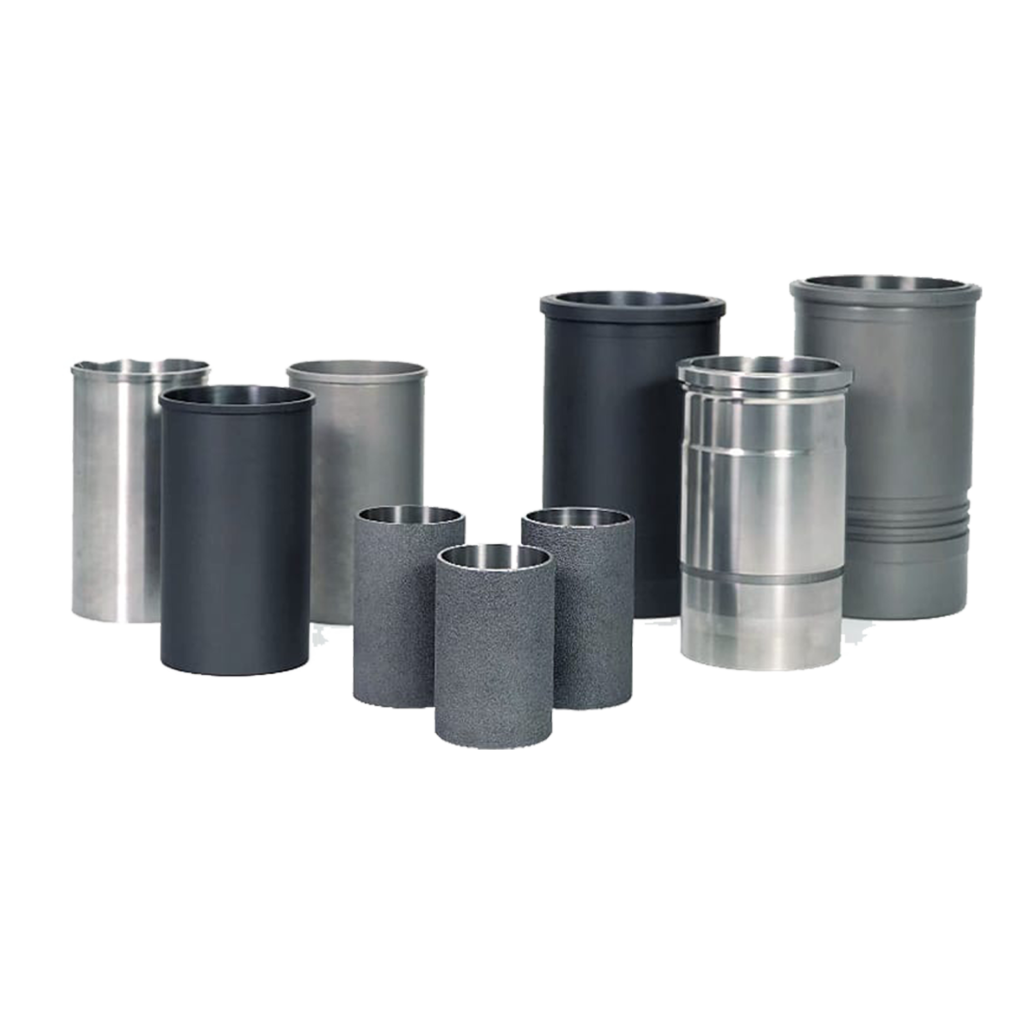
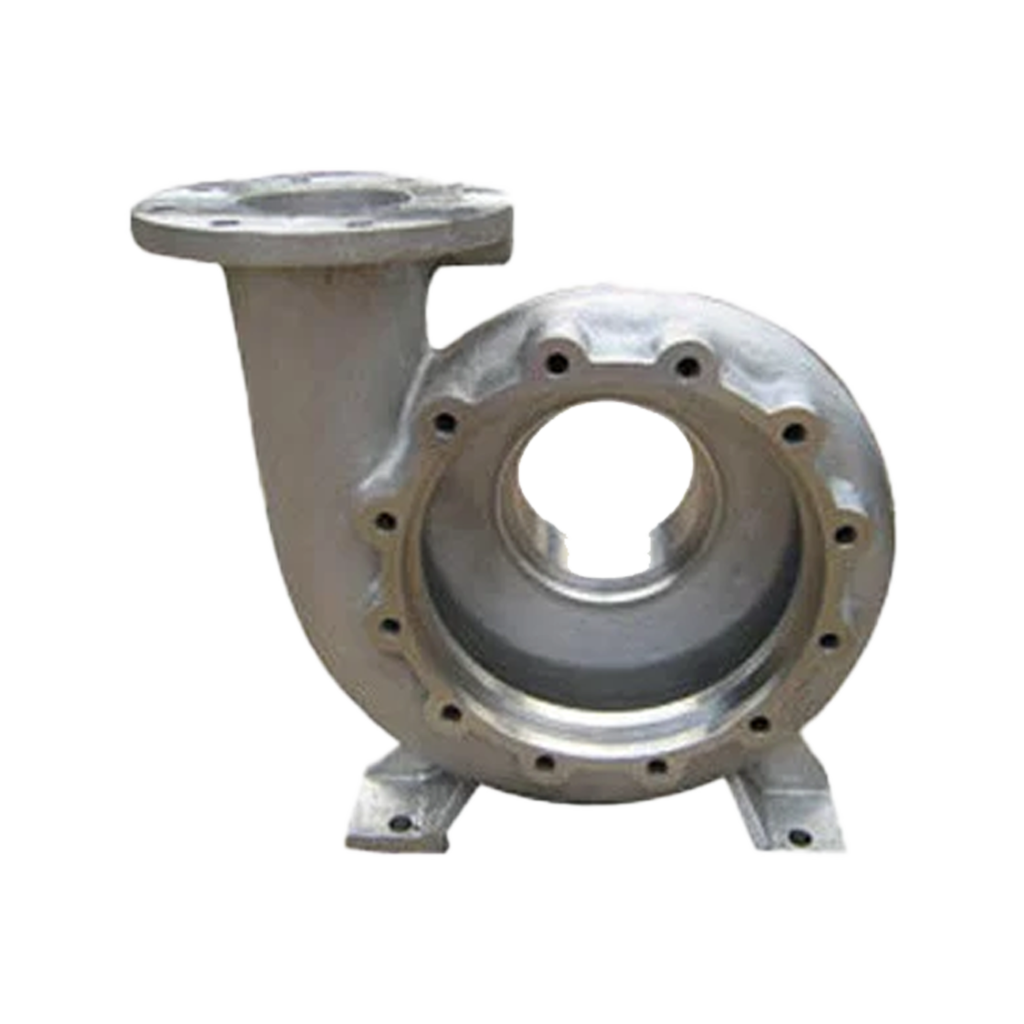
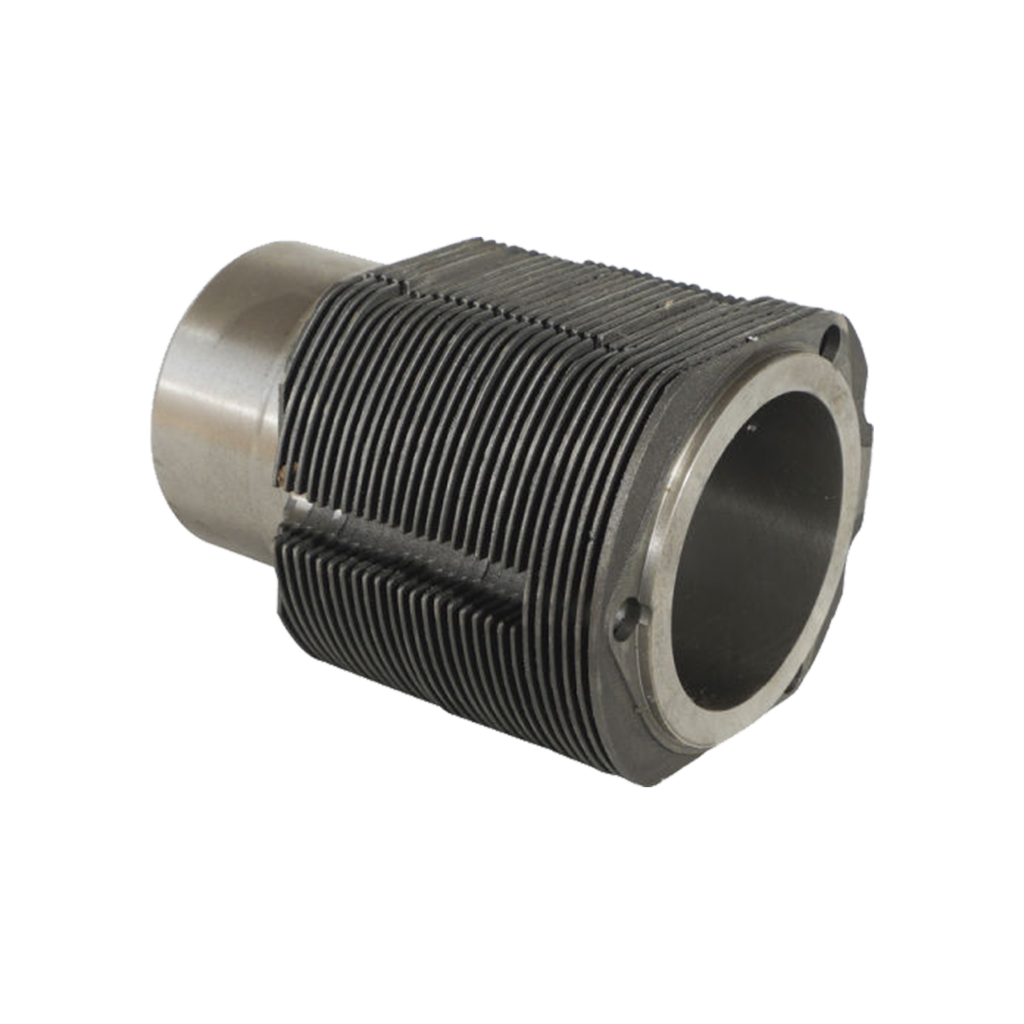
Sand Casting Process Steps at Noble Engineers
1. Mold-making – The first step in the sand casting process is to create the mold for the casting. In an expendable mold process, this step must be performed for each casting. A sand mold is formed by packing sand into each half of the mold. The sand is packed around the pattern, which is a replica of the external shape of the casting. When the pattern is removed, the cavity that will form the casting remains. Any internal features of the casting that cannot be formed by the pattern are formed by separate cores which are made of sand prior to the formation of the mold. Further details on mold-making will be described in the next section. The mold-making time includes positioning the pattern, packing the sand, and removing the pattern. The mold-making time is affected by the size of the part, the number of cores, and the type of sand mold. If the mold type requires heating or baking time, the mold-making time is substantially increased. Also, lubrication is often applied to the surfaces of the mold cavity in order to facilitate removal of the casting. The use of a lubricant also improves the flow the metal and can improve the surface finish of the casting. The lubricant that is used is chosen based upon the sand and molten metal temperature.
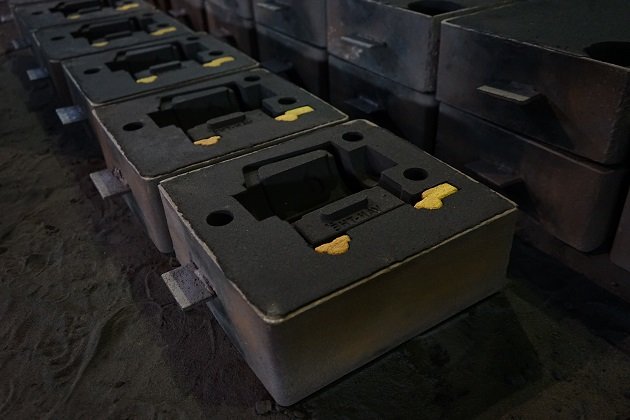
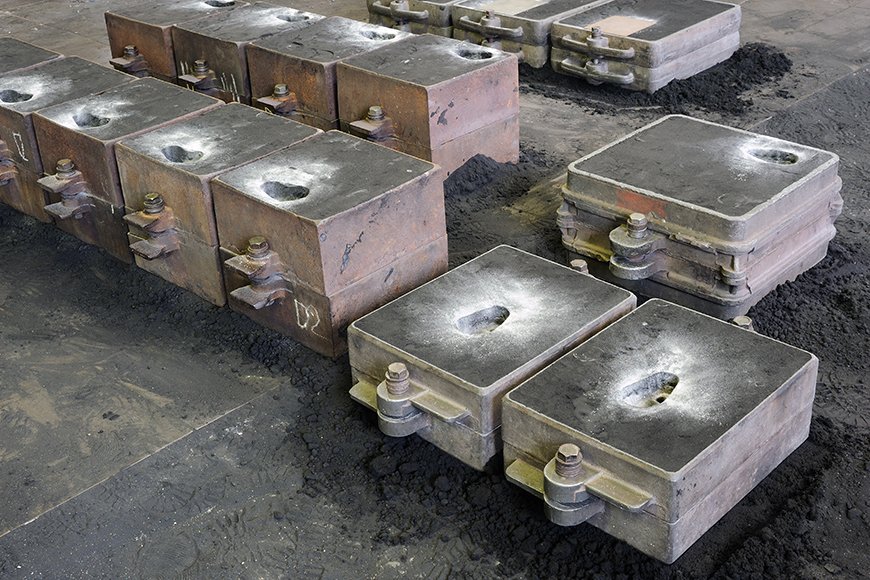
3. Pouring – The molten metal is maintained at a set temperature in a furnace. After the mold has been clamped, the molten metal can be ladled from its holding container in the furnace and poured into the mold. The pouring can be performed manually or by an automated machine. Enough molten metal must be poured to fill the entire cavity and all channels in the mold. The filling time is very short in order to prevent early solidification of any one part of the metal.
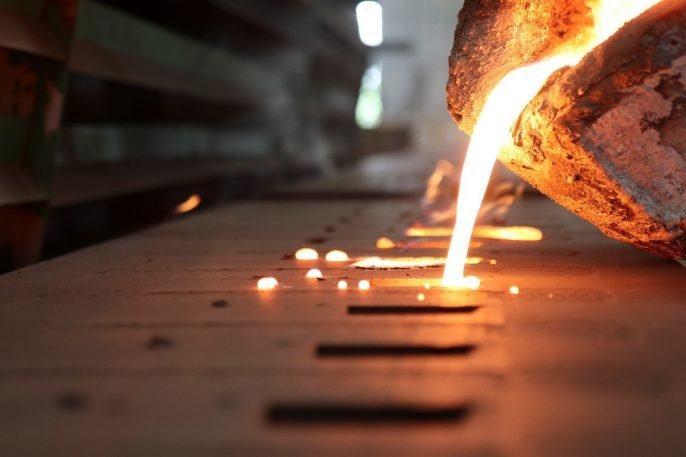
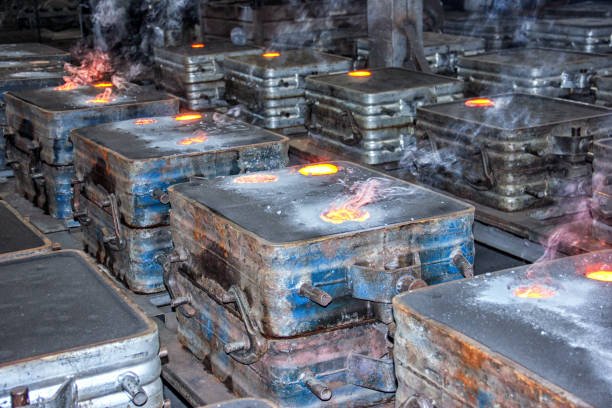
4. Cooling – The molten metal that is poured into the mold will begin to cool and solidify once it enters the cavity. When the entire cavity is filled and the molten metal solidifies, the final shape of the casting is formed. The mold can not be opened until the cooling time has elapsed. The desired cooling time can be estimated based upon the wall thickness of the casting and the temperature of the metal. Most of the possible defects that can occur are a result of the solidification process. If some of the molten metal cools too quickly, the part may exhibit shrinkage, cracks, or incomplete sections. Preventative measures can be taken in designing both the part and the mold and will be explored in later sections.
5. Removal – After the predetermined solidification time has passed, the sand mold can simply be broken, and the casting removed. This step, sometimes called shakeout, is typically performed by a vibrating machine that shakes the sand and casting out of the flask. Once removed, the casting will likely have some sand and oxide layers adhered to the surface. Shot blasting is sometimes used to remove any remaining sand, especially from internal surfaces, and reduce the surface roughness.
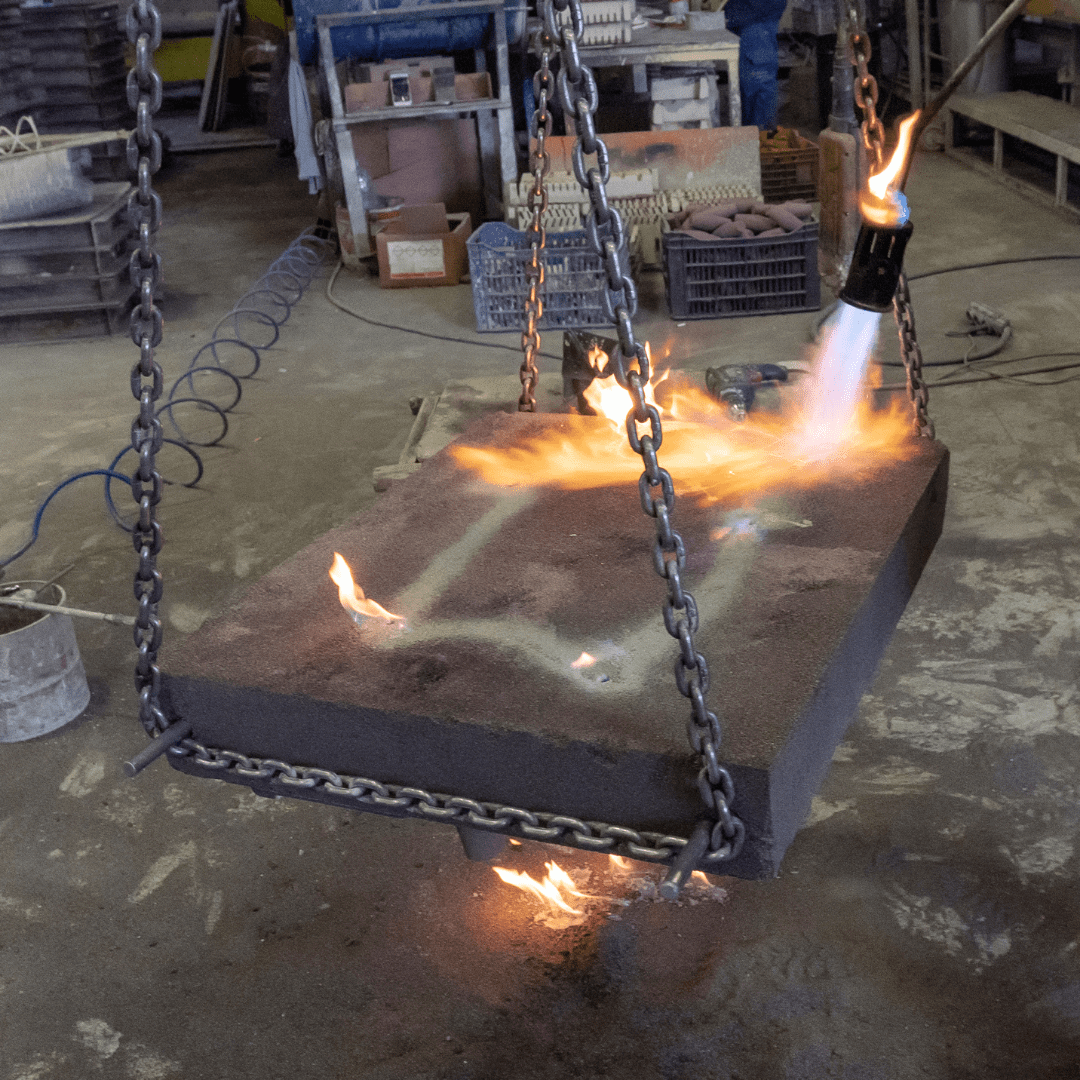
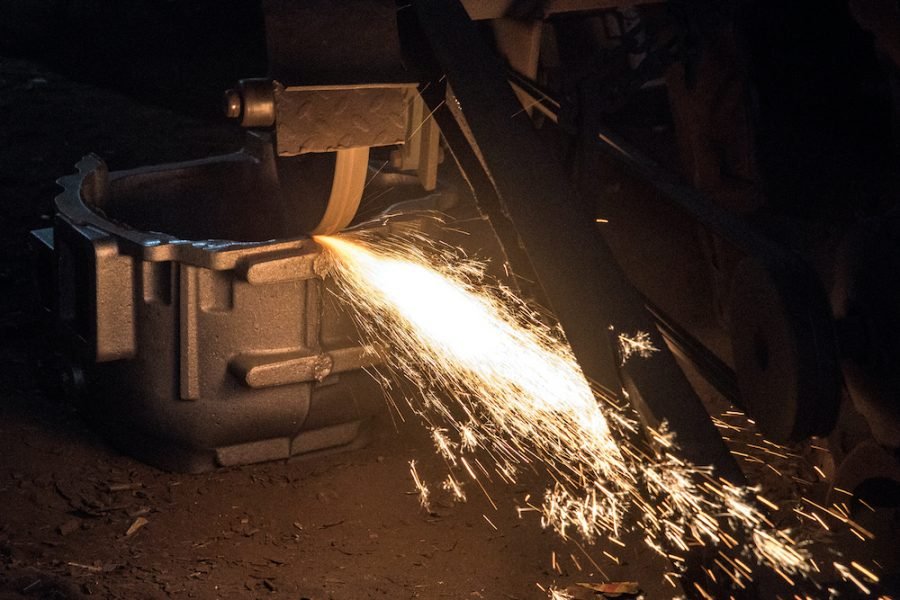
6. Trimming – During cooling, the material from the channels in the mold solidifies attached to the part. This excess material must be trimmed from the casting either manually via cutting or sawing, or using a trimming press. The time required to trim the excess material can be estimated from the size of the casting’s envelope. A larger casting will require a longer trimming time. The scrap material that results from this trimming is either discarded or reused in the sand casting process. However, the scrap material may need to be reconditioned to the proper chemical composition before it can be combined with non-recycled metal and reused.